GodlySecuritySlig
Juvelime
- Joined
- Jun 23, 2023
- Messages
- 4
- Thread Author
- #1
ROMUSDATULP -
Robotic Musculature Design and Testing for Upper Limb Prosthetics (Name Pending Rework)
INTRODUCTION
This project proposal aims to develop advanced robotic musculature design and testing techniques for upper limb prosthetics. The objective is to enhance the mobility and functionality of prosthetic limbs, specifically focusing on individuals who have lost one or both arms due to injury or medical conditions alike, highly useful in this facility all things considered. The project requires funding to support research, development, and testing phases, as well as collaboration with medical professionals in our employ and individuals with limb loss to ensure the practicality and effectiveness of the proposed solutions.
Project Overview
The loss of one or both arms not only has physical implications but also profound psychological and emotional impacts on individuals. It hampers their ability to carry out simple tasks, participate in social interactions, and pursue their passions and careers. Despite notable progress in prosthetic technologies, current solutions often fall short in replicating the intricate movements and strength of natural human limbs.
Project ROMUSDATULP recognizes the critical need to bridge this gap and revolutionize upper limb prosthetics. By harnessing the power of robotics and advanced musculature design, our aim is to create prosthetic limbs that go beyond mere functionality and truly restore individuals' sense of agency and independence. By closely mimicking the natural movement and strength of human limbs, these robotic musculature systems will empower users to engage in a wide range of activities with confidence and ease.
Through rigorous research and development, we will delve into the intricate biomechanics of human arm movements, studying the interplay between muscles, tendons, and joints. Drawing inspiration from nature's design, we will engineer robotic musculature systems that replicate the complex mechanisms at work in human limbs. By employing cutting-edge materials, innovative actuation mechanisms, and advanced sensor technologies, our goal is to create prosthetic limbs that seamlessly integrate into the user's body and respond intuitively to their intentions.
Project Benefits
The successful development of artificial musculature holds immense potential for improving the lives of individuals with limb loss or impairment. By closely mimicking the natural movement and strength of human muscles, advanced robotic musculature systems can significantly enhance the functionality and versatility of upper limb prosthetics. This breakthrough technology would empower individuals to regain dexterity, precision, and a wider range of motion, enabling them to perform daily tasks with greater ease and engage in activities that were once challenging or impossible.
Furthermore, the long-term impact of completing this project extends beyond individual benefits. The advancements made in robotic musculature design and testing can contribute to the broader field of robotics and biomechanics. The knowledge gained from this research can pave the way for the development of more sophisticated robots capable of interacting with the physical world in a human-like manner. These advancements have the potential to revolutionize industries such as healthcare, manufacturing, and space exploration, where robotic systems with enhanced dexterity, strength, and adaptability can have a significant impact.
Resources Required
Final Notes | Personnel Information
Attached to this proposal is a concept for this robotic musculature, commissioned from our art department. Like money vultures, those people..
Otto Moritz Becker IV
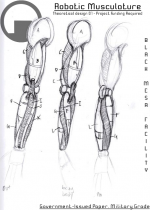
Robotic Musculature Design and Testing for Upper Limb Prosthetics (Name Pending Rework)
INTRODUCTION
This project proposal aims to develop advanced robotic musculature design and testing techniques for upper limb prosthetics. The objective is to enhance the mobility and functionality of prosthetic limbs, specifically focusing on individuals who have lost one or both arms due to injury or medical conditions alike, highly useful in this facility all things considered. The project requires funding to support research, development, and testing phases, as well as collaboration with medical professionals in our employ and individuals with limb loss to ensure the practicality and effectiveness of the proposed solutions.
Project Overview
The loss of one or both arms not only has physical implications but also profound psychological and emotional impacts on individuals. It hampers their ability to carry out simple tasks, participate in social interactions, and pursue their passions and careers. Despite notable progress in prosthetic technologies, current solutions often fall short in replicating the intricate movements and strength of natural human limbs.
Project ROMUSDATULP recognizes the critical need to bridge this gap and revolutionize upper limb prosthetics. By harnessing the power of robotics and advanced musculature design, our aim is to create prosthetic limbs that go beyond mere functionality and truly restore individuals' sense of agency and independence. By closely mimicking the natural movement and strength of human limbs, these robotic musculature systems will empower users to engage in a wide range of activities with confidence and ease.
Through rigorous research and development, we will delve into the intricate biomechanics of human arm movements, studying the interplay between muscles, tendons, and joints. Drawing inspiration from nature's design, we will engineer robotic musculature systems that replicate the complex mechanisms at work in human limbs. By employing cutting-edge materials, innovative actuation mechanisms, and advanced sensor technologies, our goal is to create prosthetic limbs that seamlessly integrate into the user's body and respond intuitively to their intentions.
Project Benefits
The successful development of artificial musculature holds immense potential for improving the lives of individuals with limb loss or impairment. By closely mimicking the natural movement and strength of human muscles, advanced robotic musculature systems can significantly enhance the functionality and versatility of upper limb prosthetics. This breakthrough technology would empower individuals to regain dexterity, precision, and a wider range of motion, enabling them to perform daily tasks with greater ease and engage in activities that were once challenging or impossible.
Furthermore, the long-term impact of completing this project extends beyond individual benefits. The advancements made in robotic musculature design and testing can contribute to the broader field of robotics and biomechanics. The knowledge gained from this research can pave the way for the development of more sophisticated robots capable of interacting with the physical world in a human-like manner. These advancements have the potential to revolutionize industries such as healthcare, manufacturing, and space exploration, where robotic systems with enhanced dexterity, strength, and adaptability can have a significant impact.
Resources Required
- Shape Memory Alloys (SMAs): These alloys, such as Nitinol, exhibit the ability to remember and recover their original shape when subjected to external stimuli like heat or electricity. SMAs are often used in actuator systems for their high force-to-weight ratio and precise control.
- Elastomers: Flexible and stretchable elastomers, like silicone or polyurethane, are employed in the fabrication of artificial muscles to mimic the elasticity and resilience of natural muscle fibers. These materials allow for controlled deformation and repeated stretching without losing their mechanical properties.
- Electroactive Polymers (EAPs): EAPs are materials that change their shape or size when an electric field is applied. Examples include conducting polymers and dielectric elastomers. EAPs offer possibilities for responsive and biomimetic actuation in artificial musculature.
- Fiber-Reinforced Composites: Composite materials consisting of high-strength fibers, such as carbon or glass, embedded in a matrix, such as epoxy or polymer, provide lightweight yet robust structures for the artificial musculature. These composites offer excellent strength-to-weight ratios and can withstand high forces.
- Biocompatible Materials: For applications involving direct contact with the human body, biocompatible materials are essential. Biocompatible polymers like polyethylene glycol (PEG) or biocompatible metals like titanium ensure the artificial musculature is safe and compatible with biological tissues.
- Conductive Materials: Electrically conductive materials like metals (e.g., copper, gold) or conductive polymers are used in the development of sensors and actuators for transmitting electrical signals and enabling feedback control.
- Adhesives and Sealants: To assemble and integrate various components of the artificial musculature, strong adhesives and sealants are required. These materials ensure secure bonding, prevent leakage, and maintain structural integrity.
- Industrial Grade Laboratory: Any laboratory rated for dangerous and mechanical objects should suffice for this. Not much else to it.
Final Notes | Personnel Information
Attached to this proposal is a concept for this robotic musculature, commissioned from our art department. Like money vultures, those people..
Otto Moritz Becker IV
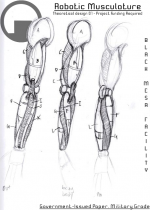
Last edited: